Acest anunț a expirat și nu este disponibil pentru aplicare
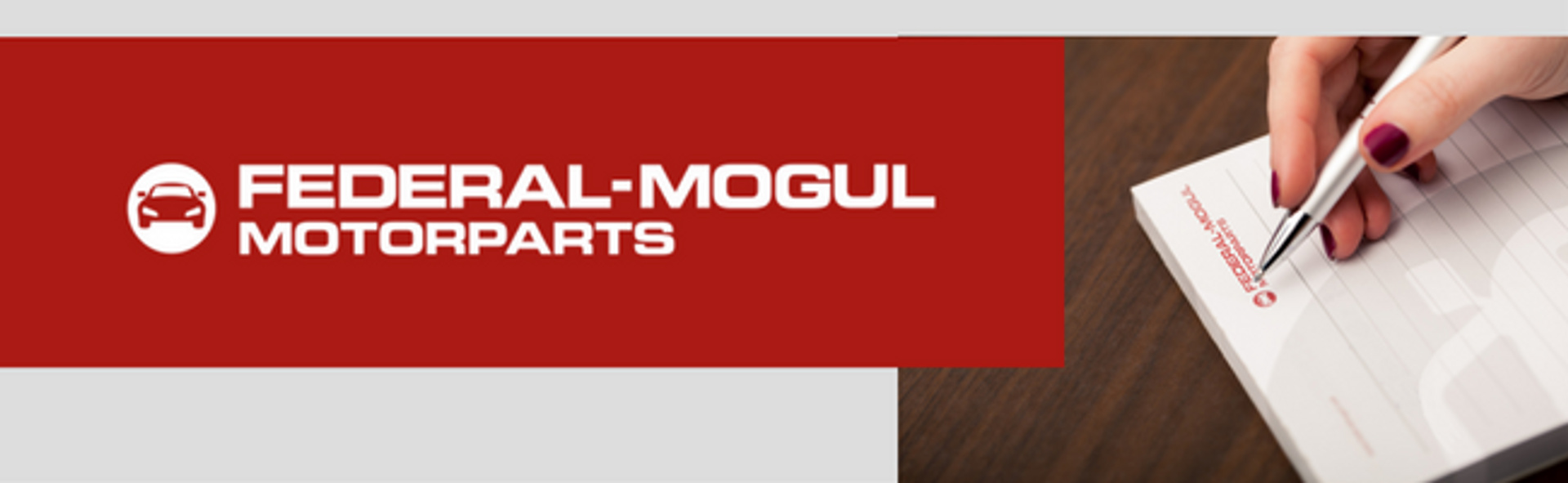
Position mission:
Coordinates the necessary activities so that the audits, inspections and quality controls carried out in the production process guarantee that the processes and products comply with the specifications.
Ensuring the quality of the production processes:
- At the beginning of each exchange, at each setup, on each production line, all the controls necessary to start the manufacture and the end of the previous batch must be executed correctly, the results reported and interpreted before batch release.
- Parameters of machines and equipment, especially those with direct influence on the critical and safety features of the product must be in accordance with the control plan
- The new control systems introduced must be approved in collaboration with the initiator of the process improvement;
- The manual and automatic product control systems already implemented must be maintained.
- Provides daily interface with Value Stream Managers to ensure the necessary resources to those described above and promptly resolve any inconsistencies found; when it is significant, it escalates the situations found to the Quality Manager and the Factory Manager.
- Participates in the audits for the approval of new or modified processes / products (MRA = Manufacturing Readiness Review) ensuring the rigor of these audits; does not allow the acceptance of production under standard conditions if the minimum conditions are not met, and the process capabilities are not at the agreed level, verifying this as soon as possible before the MRA.
- Ensures compliance with the quality procedures and the norms associated with them in the production processes;
- Coordinates in the Production area the understanding and follow-up of the findings from the external audits;
- Participates in conducting internal process and product audits performed by internal auditors;
- Organizes the verification of the internal audit process of the Production department
- Systematizes the definition and implementation of the action plans associated with the audits with the managers of the Production Department;
- Ensures periodic review of process capability for serial products together with Process Engineers;
- Block products that do not meet the specifications in the control plan;
- Supervises the internal approvals of the production processes
- Ensures the training of the operators, process quality inspectors and maintenance technicians in the field of quality;
- Supervise the recording of traceability and the flow of non-compliant parts in the process;
- Keeps track of requests for derogation on process and product quality line;
- Provides the framework for the existence of information regarding the client's specifications at the work and control stations
- Knows and is aware of the importance of its activity and of how it contributes to the achievement of quality objectives (impact on product quality, contribution to achieving, maintaining and improving quality, including consequences in case of non-compliance with customer requirement
Manage non-compliant/ inccidents:
- Coordinates the handling of the analysis of internal quality incidents, keeping up to date the action plan in the production area
- Synthesizes the status of the actions resulting from the complaints from clients and communicates the priorities resulted in the Production department, in collaboration with the Customer Quality Engineers.
- Defines, implements and monitors action plans and projects for continuous improvement of quality indicators
Reporting:
- Subordinated to the Quality Manager;
- Subordinates: Production Quality Engineers, Quality Inspectors.
Development and continous improvement of quality system:
- Coordinates the training program on quality issues and Product Safety for both subordinate staff and staff in the Production department
- Participates in the elaboration of the documentation of internal approval of the processes according to the approval procedure
- Participates in the elaboration and updating of FMEAs of product and process of production quality personnel, when their contribution is required.
- Ensures the participation of the production quality engineers in the elaboration and improvement of the control plan in collaboration with the Customer Quality Engineers, NPI Engineers and Process Engineers.
- Elaborates and improves the inspection plan after launching in manufacture with Process / Expert Engineers
Communication and reporting:
- Ensures the measurement of production quality indicators as defined by the Quality Manager and ensures their reporting in the format at the set interval, on the agreed channels.
- It is in constant contact with the Customer Quality Engineers for standardizing the good practices from other factories or to cascade the demands of the customers in production
- Verifies and proposes optimizations of measurements from production lines
Standardization and continuous improvement of the management system:
- Know and respect the Business Policy, the Internal Regulations, the Code of Conduct, the Integrity Policy, procedures and instructions specific to the area of activity and other procedures in which it has responsibilities
- It contributes to the continuous improvement of the results / performances of the department, constantly identifies - opportunities for improvement of its own activity and activities of the unit (Kaizen ideas / month according to the factory objectives).
- Ensures the application of the Change Management process, with the corresponding approvals and registrations, when initiating a change with impact on the product, process, SSM risks, quality, layout, equipment, infrastructure, etc.
- Performs spontaneous or scheduled audit activities (Gemba Walks, 5S audits) and identifies opportunities for improvement
- Participates in the meetings for analyzing the results and activity specific to the job level (dailyand / or - as appropriate, weekly / monthly meetings, etc.)
- Take actions to implement the specific requirements of FMOS policies and procedures and integrated management of quality systems, SSM within its own department
Requirements:
- University degree (technical);
- minimum of 5 years experience in quality automotive, preferably in shop-floor quality roles, and in 2 years in a people management role;
- knowledge of core quality tools and 6 Sigma;
- proficiency in English language.
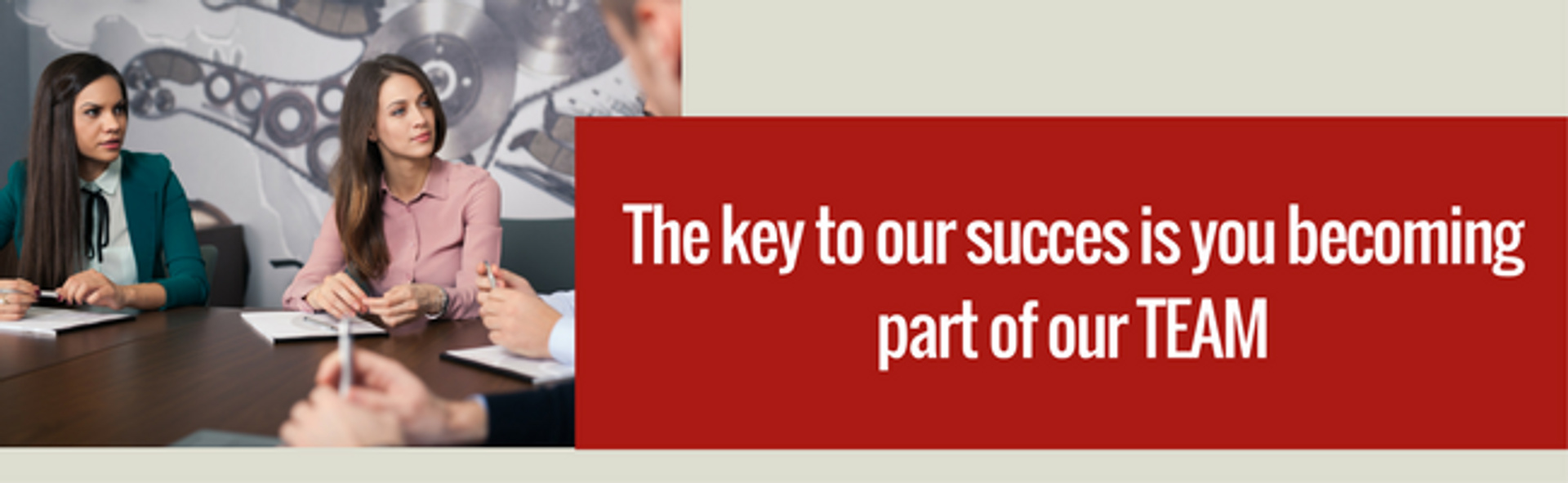